- Share
- Share on Facebook
- Share on X
- Share on LinkedIn
Objectives
The electrospinning process involves applying a high electric field, which can reach 5,000 V/cm, between a polymer solution and a collector. Under the influence of the electric field, a jet of viscoelastic fluid is emitted from the tip of the hanging droplet (Fig. 1 a). Charged on the surface, this jet is accelerated and stretched (Fig. 1 b). The solvent evaporates in the first few centimeters of the jet's propagation in the air, resulting in a nanofiber of polymer collected on a substrate (Fig. 1 c).
This method allows for the fabrication of fibrous materials with a surface-to-volume ratio on the order of approximately 10e6 and an open porosity exceeding 80%. Such materials can be functionalized on their surface to impart new properties for various applications. Relative to their mass, they exhibit mechanical properties significantly superior to their bulk counterparts, in terms of Young's modulus and strain at break.
These nanofibrous materials find applications in numerous industrial sectors such as tissue engineering, filtration, technical textiles, catalysis, energy (membranes for fuel cells), and detection (sensors).
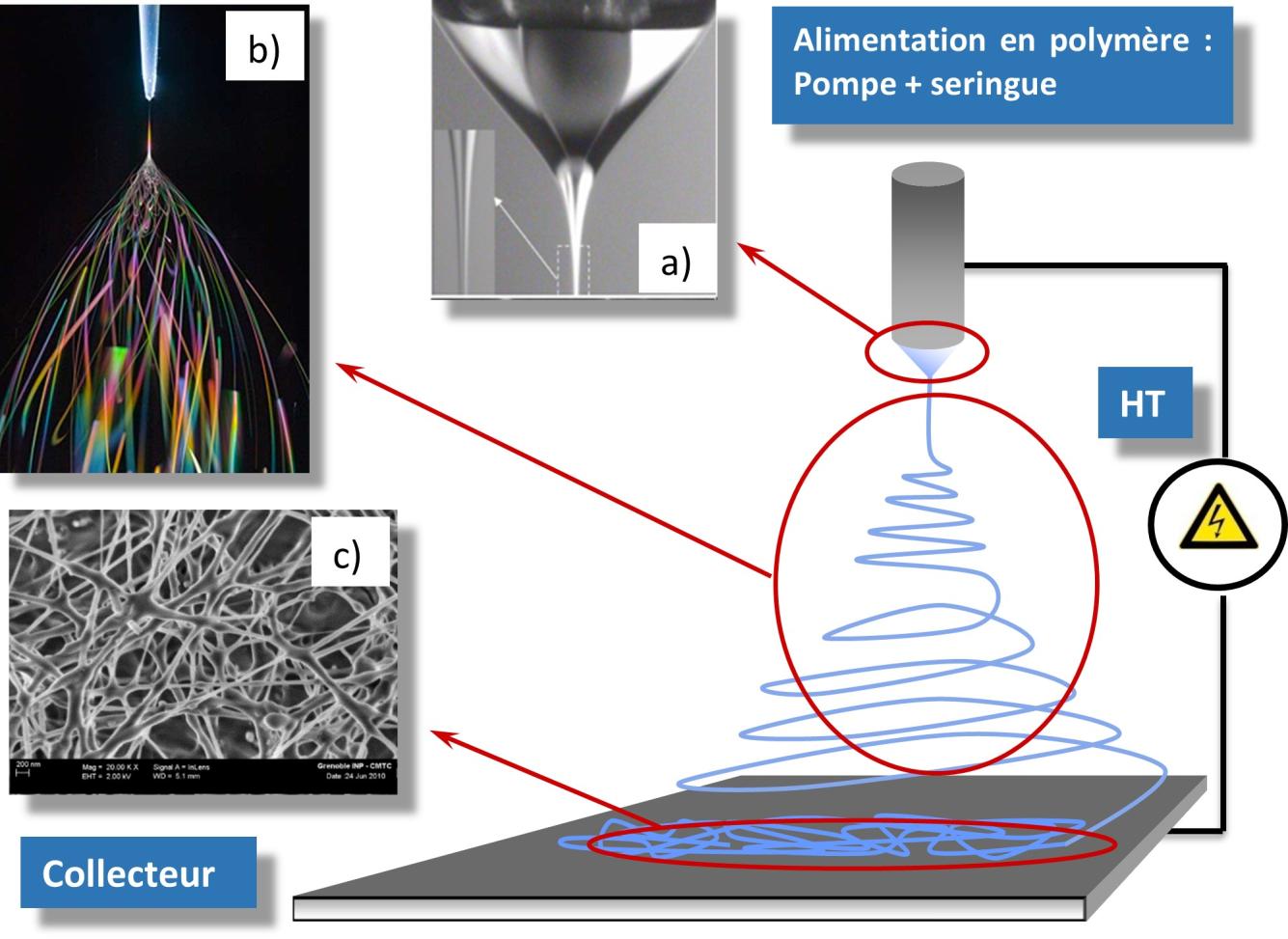
Results
Structuring of Nanomaterials
Controlling the structuring of the fiber network allows for the mastery of the material's mechanical properties. One method involves depositing fibers onto a rotating cylindrical collector (Fig. 2). The rotation speed of the collector enables both the control of the degree of fiber alignment and their diameter (Fig. 3).
Structured collectors have been designed and fabricated, featuring peaks arranged in a way that creates repetitive patterns on their surface. These peaks locally modify the electric field and enhance the attraction of fibers to these points (Fig. 4).
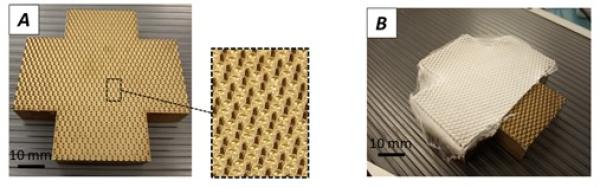
Mechanical Characterization of Structures
The anisotropic nature of the materials obtained is characterized by tensile tests in two perpendicular directions. This mechanical anisotropy is coupled with morphological characterization of the network during tension (Fig. 5).
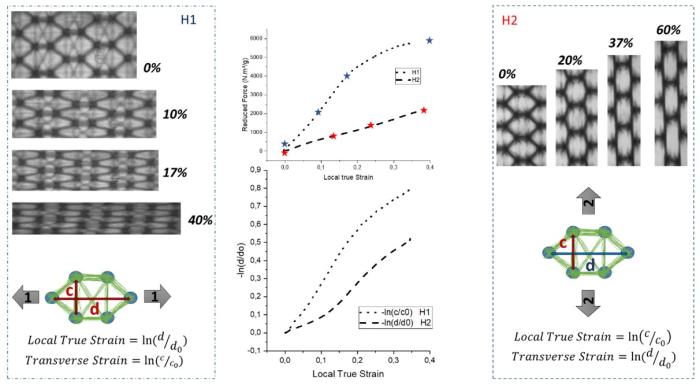
References
-
H. Mondésert, F. Bossard, D. Favier, "Anisotropic electrospun honeycomb polycaprolactone scaffolds: Elaboration, morphological and mechanical properties", journal of the mechanical behavior of biomedical materials 113, 2021, 104124; https://doi.org/10.1016/j.jmbbm.2020.104124
-
L. Gangolphe, C.Y. Leon-Valdivieso, B. Nottelet, S Déjean, A. Bethry, C. Pinese, F. Bossard, X. Garric, " Electrospun microstructured PLA-based scaffolds featuring relevant anisotropic, mechanical and degradation characteristics for soft tissue engineering", Materials Science & Engineering C 129, 2021, 112339; https://doi.org/10.1016/j.msec.2021.112339
- Share
- Share on Facebook
- Share on X
- Share on LinkedIn